中小企業とDX
「品質・コスト・納期を別次元に引き上げ」 徹底的なスマートファクトリー化を推進【株式会社丸秀(東京都大田区)】
2023年 5月 15日
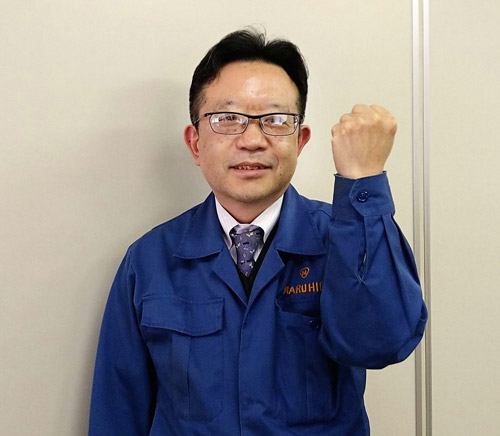
自動車業界は大きな変革期を迎えている。脱炭素社会の実現に向けてガソリン車からEV(電気自動車)へのシフトが世界的に加速。その荒波は自動車部品メーカーにも大きな影響を及ぼすことが予想されている。自動車のトランスミッション部品などを加工製造する株式会社丸秀は、IoT(モノのインターネット)を活用し、徹底的なスマートファクトリー化を推進。DXセレクション2022の認定企業に選ばれた。
加速するEVシフト「特効薬がみつからない」
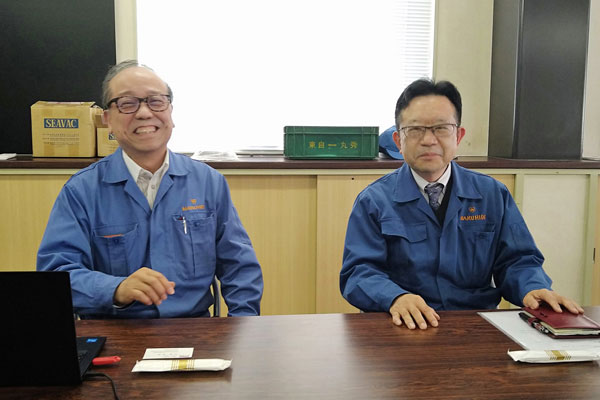
「当社の売り上げの3割は乗用車のトランスミッション部品。EV化でこの分野の売り上げが今後、大幅に減ることが予想された。対策を議論したが、特効薬はみつからない。会社の体質を強化しかない。そういう結論に達した」。丸秀代表取締役の小林隆志氏は徹底的なDXに取り組んだ理由をこう説明した。
丸秀は1947年に小林氏の祖父が創業した。小林氏は、二代目の父から2004年に経営を引き継いだ。売り上げの主力はバス・トラックなどの部品製造で売り上げの約6割を占めている。金型設計製作からプレス加工、機械加工、溶接、塗装、組み立てまで自社内設備で一貫生産が可能で、1個の小ロット生産から月10万個の大量生産まで顧客のニーズに合わせて生産できる。
創業者の出身地である山形県長井市に設けた3つの工場が生産拠点となっており、1日当たり3000種類もの部品を顧客に納入している。取り扱う部品点数は1万2000点にも及ぶという。「取引先からはうちに出せば試作から量産まですべてこなせると高い評価いただいている」と小林氏は胸を張った。
バス・トラックの部品製造の技術を磨き上げ、精密な加工技術が求められるトランスミッション部品の分野に参入。売り上げの二番目の柱になるまで成長させた。だが、EVシフトはそんな長年にわたって築き上げた事業基盤を揺るがしかねない一大事だった。EVは基本的にトランスミッションを必要としないためだ。最悪の場合、売り上げの3割がゼロになる。小林氏は取締役工場長の新井康司氏と対策の議論を重ね、導き出したのが「IoTを活用し、QCD=Quality(品質)、Cost(コスト)、Delivery(納期)=を別次元に引き上げることへのチャレンジ」(小林氏)だった。
「IoT 5カ年計画」を策定 工場の電子化を推進
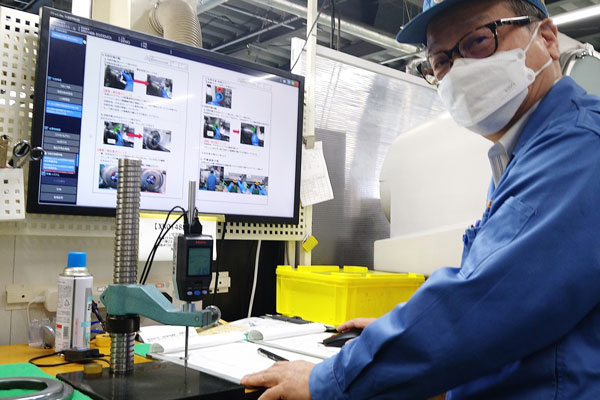
改革の先頭にたったのが新井氏。過去に自動車メーカーに勤務していた経験を活かし、改革のデザインを描いた。県や金融機関などが開催するIoTの勉強会を巡り回った。そして工場のQCDを上げるのに何が阻害要因になっているのか、徹底的な洗い出しを行った。
「少量多品種の部品を扱っているため、装置の組み替えが頻繁に行われる。組み替え中、機械が稼働できない。工場内の情報が紙で管理されていて、データ分析力も弱かった」と新井氏は振り返る。雇用の逼迫も阻害要因の一つとして持ち上がった。
「QCDの別次元への引き上げ」を目指して策定したのが「IoT 5カ年計画」だ。「現場情報の電子化」「稼働状況の見える化」「第三工場のスマートファクトリー化」という3つの改革の柱を立てた。
これまで丸秀では、機械のセッティングなどの生産現場の作業情報はすべて紙でやりとりされていた。1日3000種類もの部品を製造するため、1つの製造装置で金型を何度も交換する。作業手順をまとめた紙を管理しているファイルから取り出し、その紙を製造装置のある場所に持っていって作業する。製造した部品の検査工程もすべて紙に記録をしていた。
そこで取り組んだのが現場情報の電子化だ。紙の資料をすべてデータ化し、それを機械のそばにあるモニターで確認できるようにした。作業がすばやくできるよう注意点などの画像も添えられた。製品検査に使用する計測器はすべてネットワークに接続した。部品を計測器にセッティングし、得られた検査データは、ボタンを押すと社内のサーバーに蓄積される。検査台にはカメラを設置。不具合部分がみつかると、すぐにカメラで撮影する。
「これまで検査の結果を手書きで記入していたが、工数が多く、誤記入もあった。データを統計的に処理しようとすると、表計算ソフトに再入力してグラフ化する。非常に工数がかかったが、大幅な省力化が実現できた」と新井取締役は話す。
さらに計測器だけでなく、プレス機などの製造機器もすべてネットワークに接続し、製造装置の稼働状況をリアルタイムで電子データとして蓄積する。いつ、誰が、どれくらいの時間で、どんな作業をして、どれだけの部品を製造したという作業履歴も電子データで記録できるようにした。
自前でデータを「見える化」、分析して業務を効率化
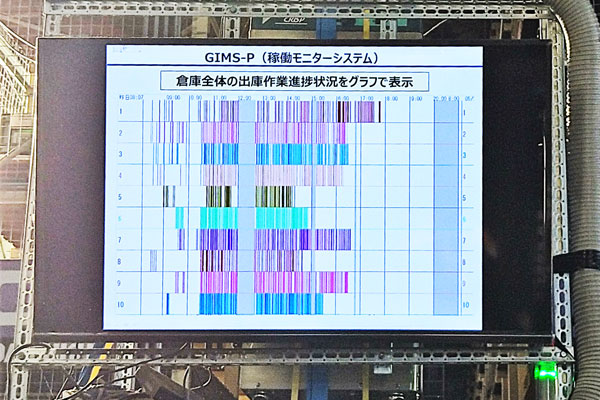
集めたデータを分析しやすいよう「見える化」するためのソフトウエアは自前で開発した。
新井氏は社内のITに詳しい5人を人材選び、DXのコア組織を兼務させた。地元のシステムエンジニアと連携し、データ分析のためのソフトなどをシステムの基礎部分のプログラミングをエンジニアに依頼する一方、細かい操作性にかかわる部分は5人のスタッフが受け持った。
開発したシステムを導入すると、決まって作業スタッフから「今までの方がよかった」といった反発を受けたという。そんなシステムを利用する従業員の声にもしっかりと耳を傾けた。「この部分が使いにくい」「こうしてほしい」。そんな要望に対応して、5人のスタッフがシステムを改良した。「繰り返し修正していくと、反発のしようもなくなる。自社で開発しているので、改良もしやすい。そこは内製化のいいところ」と新井氏は目を細めた。
データの分析によってどんな改善につながったのか。新井氏はこう説明する。
「同じプレス機を使って同じ部品を製造する工程を調べると、作業にかかる時間や品質が人によってばらつきがあった。材料を機械に送り込む際、熟練した作業員はうまく工夫して手早く送り込んでいたが、経験の少ない作業員は不良品を出さないよう慎重に材料を送り込んでいた」
対策として講じたのが、材料送り込むガイドの改良だった。従業員の腕にかかわらず誰もが効率よく作業できるようにガイドを改良した。すると、人による作業のムラは少なくなり、生産性は飛躍的に向上した。こうした改善の取り組みは、情報を電子化し、稼働状況を「見える化」したことによって生まれた成果だ。
内製化は導入コストの抑制にもつながっている。
最近は、システムの管理にクラウドを活用する企業が多いが、丸秀では自社サーバーで管理する方法を選択した。「その方が、コストがかからない」と新井氏は指摘する。計測器のネットワーク化はもともと機器に搭載されている機能を活用した。ソフトウエアの開発では、基本ソフトをオープンソースになっているLinux(リナックス)をベースに構築し、費用を抑えた。工作機械のネットワーク化するためにすべての装置にマイコンボードを組み込んだが、一般的に販売されている数千円程度の汎用品を活用した。
デジタル人材育成を強化、QCDが飛躍的に向上
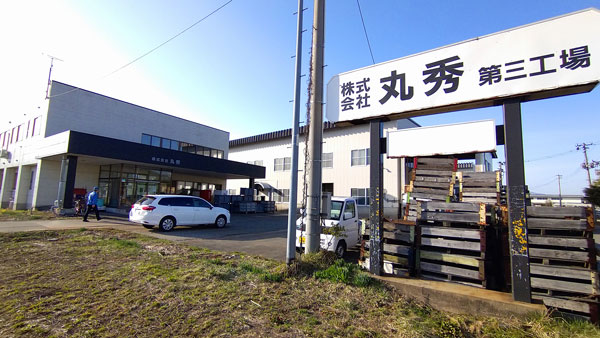
DXに対する従業員の理解を深めるための取り組みにも力を入れている。
管理職・リーダークラスの職員を中心に表計算ソフトや品質管理の基本、問題解決の見つけ方といったテーマで研修を実施。DX推進するうえで必要なスキルを養成するとともに社内へのDXの浸透を図っている。また、DX担当のコアスタッフも拡充。デジタル技術を持つ人材を外部からも採用し、現在は12人に増えている。
計測結果や稼働データが自動的に収集できるようになったことと、データを活用できる人材が育ったことでQCDの改善が大幅に進んだ。
品質に関するトラブルの件数は、計画以前に比べ6割も削減された。世界の主要自動車メーカーが導入する自動車産業に特化した品質マネジメント規格「IATF16949」の認証取得にこぎつけることができた。
コストの面では、生産部門で15%、間接部門で3割の労働力削減につながっている。また、金型の製作時間も約3割短くなるなど納期のスピードアップに結びついている。
スマートファクトリーにチャレンジ
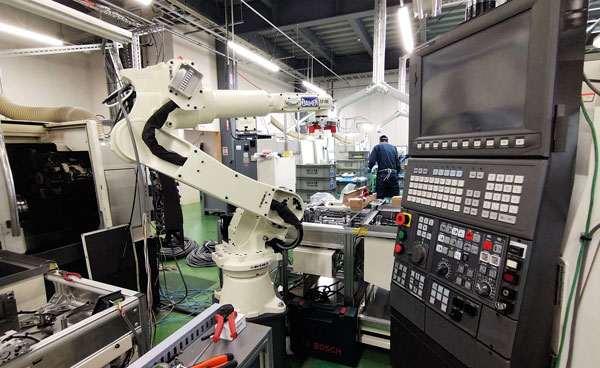
現在は、「5カ年計画」の第3の柱である「スマートファクトリー化」に向けた取り組みを遂行中だ。
長井工場には3つの工場があるが、自動化を進めているのは、トランスミッション部品を製造する第三工場。生産工程にロボットのラインを設置したほか、工場内での部品や材料の搬送を無人で行う自動搬送するシステムの構築を進めている。
2021年に稼働した第1号のロボット・ラインでは、CNC旋盤による部品の加工からさび止め油のどぶ付けまでの工程を2台のアーム型ロボットが行う。これまで同一の工程に12、13人の要員が必要だった作業は2、3人で済むまで省力化された。自動化にあたっては、汎用のロボットを導入。部品や材料をつかむアタッチメント部分を、自社の加工機械を駆使して内製し、導入コストを抑えた。
新型コロナウイルスの感染拡大や半導体部品の不足の影響などからスマートファクトリー化は、計画に遅れが出てしまったが、1号機の稼働にめどがつき、現在は2号機の開発中だ。「人からロボットへの工程の変更は顧客の承認も必要。承認を受けた段階で、2号機、3号機を導入し、工場全体に広げていきたい」と新井氏は意気込みをみせた。
DX化を推進した丸秀のチャレンジは、他の中小企業では、なかなか真似のできないことのようにもみえる。だが、一般的に流通している汎用品をうまく活用し、コストの低減を図るなど参考にすべきポイントが数多くちりばめられている。小林氏は「まずは会社で何が困っているかをあぶり出すことが大事だ。そこから取り組むと、DXにとりかかりやすい」とアドバイスしている。
企業データ
- 企業名
- 株式会社丸秀
- Webサイト
- 設立
- 1950年4月
- 資本金
- 8000万円
- 従業員数
- 200人
- 代表者
- 小林隆志 氏
- 所在地
- 東京都大田区多摩川1-21-5
- Tel
- 03-3759-7766
- 事業内容
- トラック・バス・フォークリフト・建設機械などの輸送用機器部品製造、乗用車のトランスミッション部品製造など