BreakThrough 企業インタビュー
常識を覆した発想の技術開発でマイクロ精度部品製造技術を完成させた【株式会社小松精機工作所】
2019年 3月 14日
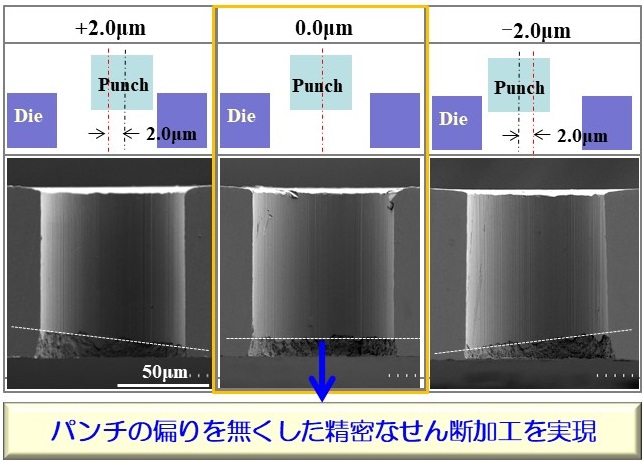
summary
唯一無二の技術で新事業展開
「無いものは創る」の精神で技術のデパートを目指す
プレス加工は、金属部品を安価で大量生産することに秀でた製造法であり、分野を問わず、製造業には欠かすことのできない基盤技術だ。
プレス部品の成形で必ず使用され、プレス加工における基本工法といっても過言ではないのが、雄型であるパンチと雌型であるダイの間に材料を挟み、押圧して材料を分離させるせん断加工だ。せん断加工で分離した材料の側面には、だれやせん断面、破断やかえりが形成されるが、これらは成形する部品の精度や機能を決める重要な要素となる。より高精度な部品を加工するには、だれは小さく、せん断面は長く、かえりは最小限に留める必要がある。そのために重要になるのが、パンチとダイの隙間である“クリアランス”だ。高精度を実現するためには、このクリアランスをできるだけ小さく調整する必要がある。
従来、クリアランスの調整は金型職人の手作業というアナログなプロセスで行われており、その精度は±1μm(マイクロメートル。1/1,000mm)が限界だった。この金型の位置合わせをデジタル調整に変換することで、ナノメートル精度を確保できるナノメートル精度デジタルクリアランス調整金型を開発したのが株式会社小松精機工作所だ。
開発成功に至るまでの経緯
研究開発部研究開発課課長である白鳥智美氏は「ナノメートル精度の金型位置合わせは、同社だけが取得している技術だ」と語る。
「マイクロ加工」とは、本来、工具の精度や加工部品の単位を1μm単位で管理する技術を指す。しかしながら、先述の通り、職人の手作業による機械加工や位置合わせには限界があり、1μm単位のばらつきが発生してしまうのが実情だ。そのため、これまでは「マイクロ加工」とは呼ぶものの、このばらつきを許容するような形で対応が取られてきた。
そこで同社は、金型内にピエゾ式ステージ(位置検出センサ)を組み込むことで、クリアランスの調整をデジタル調整に変換するデジタルクリアランス調整金型を開発。クリアランスの調整精度を従来のμm単位から2桁小さい10nm(ナノメートル。1/100,000mm)単位にまでに高めることに成功した。
現在、この金型を使用して被加工材の結晶粒変形状態の可視化定量化を進め、せん断加工条件の最適化探査を行う受託事業を展開している。
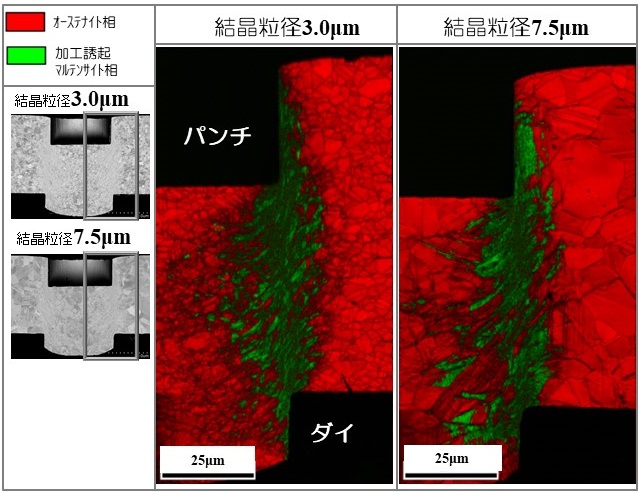
産学官連携でイノベーションを
金型位置合わせの精度は、30年来マイクロメートル単位が限界であり、機械の弱点を職人が補うというのが金型の世界の常識だった。そんな業界の一般常識に正面から挑み、アナログのノウハウをデジタルに切り替えた、というところに同社の底力が感じられる。
金型という、金属を変形させるほどの力が加わる状況で、デジタルなステージが荷重に耐えられるようにすることは容易ではない。経済産業省が支援する戦略的基盤技術高度化支援事業の採択を受け、(国研)産業技術総合研究所や首都大学東京などの研究機関、圧延材加工事業社らと協業して開発を進めた。白鳥氏いわく、「想定荷重を限定しながら、荷重に耐えられる工夫を産学官連携で進めたことが成功につながっています。」とのことだ。
外部発信で新規顧客獲得へ
ナノメートル精度の加工技術のニーズは広いものではない。だからこそ、確実に伝えていきたいと、展示会への出展や論文発表など、外部への技術発信を積極的に進めている。
この結果、新規顧客から予想外の要望を受けたケースもある。同社のナノメートル精度金型を用い、新規顧客の部品評価を進めてしてほしいというものだ。現在、自動車部品会社、大手電機機器メーカーなど複数の企業と加工現象の解明が進行中。ナノメートル精度の金型を用いた加工現象解明を顧客と共に進めている。
図面を預かり製品を実現させるというプロセスから、顧客が困っている加工現象を解明する試験受託まで、業務の幅が広がったのだ。部品を実現する前の原理、自社では取り扱いのなかった原料や技術などを目にすることで、未経験の材料や条件でも試験を請け負える会社へと成長できた。
「世の中に存在しないものを作り上げる取組みを、図面を作る前からお客様とご一緒できています。開発者としては幸せです。」と、白鳥氏は語る
新しい出会いから新しい技術が生まれる
「今後も基本は変わらないですし、変える必要性はないです。」と白鳥氏。同社の特長は、腕時計部品製造で培った、極小のエネルギーで駆動する高精密部品の製造技術。そして、「無いものは創る」というチャレンジ精神だ。創業時は腕時計部品の組立であった同社の事業は、プレスによる時計部品の自社製造を始まりとして、電子部品の製造、自動車部品の製造へと拡大を辿り、海外進出も果たした。
今後も、事業を拡大していく中で獲得したプレス加工、機械加工、レーザー加工などの一般的な技術から、拡散接合などのニッチな技術まで、技術のデパートとしてお客様の困りごとを解決し、開発・試作・量産までを担うものづくりと開発を進めていくとのことだ。
「新しい出会い、新しい素材から新しい技術のヒントを得ることができます。開発ニーズの先取りが重要です。」
マイクロ加工を扱う企業はまだまだ少ない上、同業者間で共通の課題も多いのが現実だ。企業間や産学官の連携で技術を向上させ、個別の企業の利益はもちろん、技術の社会適用拡大による産業振興を目指している。
企業データ
- 企業名
- 株式会社小松精機工作所
時計部品や燃料噴射部品製造で培ったマイクロ部品の量産加工技術を基盤として、次世代を切り開く加工技術の開発を進めています。
取材日:2019年2月1日