生産性を考える-IoTとものづくり企業-
IoTで炉の稼働状況を遠隔監視「岡谷熱処理工業」
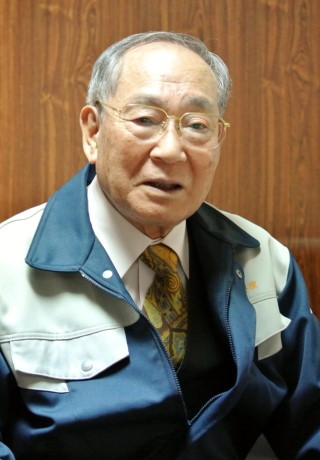
金型や工具などの金属製品を熱処理とコーティングによって強靭化、長寿命化するメーカー。夜間に無人で稼働している熱処理炉・コーティング炉の稼働状況をスマートフォンでリアルタイムに遠隔監視できるシステムを開発、導入し、管理者の負荷を軽減するとともに停電等による炉内温度の変化など稼働ミスの発生を軽減した。同時に、営業業務のOA化も進め、受注票作成作業を効率化した。前例にとらわれずにチャレンジすることを信条に、新技術を次々と開発しており、2017年末には「地域未来牽引企業」に選ばれた。
熱処理炉内の状況をスマホで確認
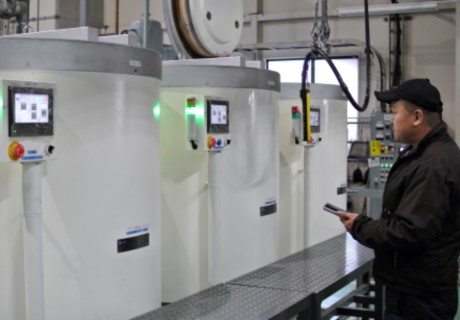
「これまでは雷が鳴ると、夜中でも工場長が熱処理炉・コーティング炉を点検するために工場に駆けつけていましたが、今は自宅に限らずどこからでも炉内の状況を確認できます」。
精密機械工業が集積していることから「東洋のスイス」と呼ばれる諏訪湖周辺地域に立地する岡谷熱処理工業。同じ形の熱処理炉が5基並ぶ前で、西澤邦治(にしざわ・くにじ)代表取締役社長(77)はこう語る。工場長が手にしているスマートフォンの画面を見せてもらうと、熱処理炉に取り付けられた操作盤の画面と同じ数字が並んでいる。
同社が行っている熱処理とコーティングのうち熱処理を例にとると、この熱処理炉は正確には「焼き戻し炉」という。プレス用金型や工具などの材料である鋼(こう=はがね)は「焼き入れ」と「焼き戻し」の2つの熱処理をすることによって鋼本来の特性が得られる。「焼き入れ」は鋼を硬くするための熱処理で、一定の温度で加熱してから冷却する。「焼き戻し」は、焼き入れを終えた鋼の硬さを調整し、ねばりを引き出すとともに内部の歪みを除去するために行う。一般的に硬さを追求するときには低温、粘り強さ(靭性)を追求するときには高温の焼き戻しを行う。
同社では通常、深夜12時頃までは夜勤の作業者が熱処理炉の稼働状況を監視しているが、それ以降は工場内に誰もいない状態で熱処理炉を運転している。熱処理炉に流れる電流が10分の1秒瞬断されただけでも、炉内にある金型などの品質が劣化したり、納期が遅れたりするので、何らかのトラブル発生が予想されるたびに工場長らが駆けつける必要があった。
こうした夜間における稼働管理の負荷を低減するため、同社は2016年、新規導入の真空焼き戻し炉2基と既設の焼き戻し炉3基の合計5基をIoT化。スマホでリアルタイムに炉内の稼働状況を監視し、異常が発生したときには緊急停止できる仕組みを構築した。これら5基の焼き戻し炉は炉内温度をはじめファン回転数、使用電力量、各アラームをスマホの画面に表示でき、新設の真空焼き戻し炉はこれに加えて炉内真空度や冷却水温度も表示できる。いずれの炉も、工場内外のどこにいてもスマホで監視・非常停止することができる。セキュリティー確保のため、アクセスした人の名前もわかるようになっている。
熱処理炉メーカーの技術共通化を望む
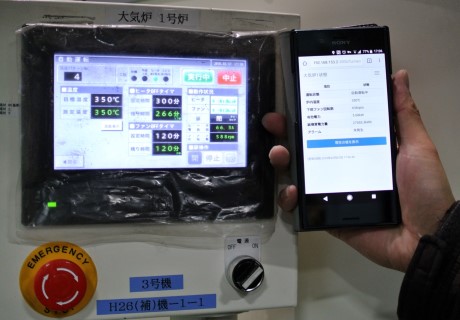
西澤社長はこうした遠隔監視・制御が可能になったことにより、工場長らの負荷軽減のみならず、「炉の異常運転や故障による品質劣化や納期遅れが防げるようになった」と強調する。炉の稼働データは常時、熱処理炉メーカーに送られるので部品の交換時期・オーバーホール等を正確に把握できるなどメンテナンスの確実性も高まった。焼き戻し炉のIoT化に際しては、経済産業省の「平成27年度補正予算 ものづくり・商業・サービス新展開支援補助金」を活用した。
同社には全部で40基近い熱処理炉があり、他の炉も段階的にIoT化していく考えだ。ただ、複数のメーカーの熱処理炉を使っているため、IoT化するには一つのスマホアプリで操作できるように、各炉の監視・制御関連技術を共通化する必要があるが、すでにIoT化した炉のメーカーを除いて、他のメーカーは共通化に消極的で、それがネックになっているという。
受注票の作成もOA化
一方、同社は営業担当者による受注票の作成作業もOA化した。同社は通常、営業車両9台で長野県とその周辺地域に散在する顧客の工場を巡回し、顧客から金型などの製品を預かってくる。従来は、営業担当者が会社に戻ってから、受注票を手書きし、熱処理を行う炉の選定をはじめとする加工工程を決めていた。
それがOA化した現在は、営業担当者が顧客先で受注票に製品の種類や鋼の種類、指定された硬さなどを記入し、スマホなどで撮影した製品の写真と一緒に本社にインターネット回線を利用して送れるようになった。本社では、送られてきた受注票と写真の内容をパソコンにインプットすると、どの熱処理炉・コーティング炉をいつから利用すればいいかといった加工処理の段取りがわかる仕組みだ。これにより、受注してから加工工程に入るまでの作業を大幅に短縮できた。また、受注データの集積・管理が簡単にできるので、将来的にはAI(人工知能)を活用して、加工工程の一層の効率化はもちろん、経営分析にも役立てていこうと考えている。
常識にとらわれず新技術にチャレンジ
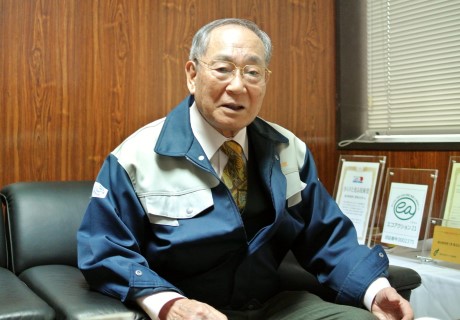
「これからも、少子高齢化が進む中で、どのようにして機械化を進め、生産性を高めていくかということを考えていかなくてはいけない」。
こう語る西澤社長は、もともと旧日本電信電話(現NTTグループ)の技術系サラリーマンだった。電報電話局長のときに鋳物会社にスカウトされ、そこの営業担当として岡谷熱処理工業を訪れたのが縁となった。創業者の先々代社長に後継者として見染められ、その跡を継いだ奥さんからも重ねて勧誘されて、60歳になった2002年に副社長として入社。翌年に社長に就任した。以来、企業理念の一つにも掲げている「本質を考えよう 前例に頼らず」を信条に、従来の常識にはとらわれない新技術の開発にチャレンジしてきた。
その一つが「平成21年度補正ものづくり中小企業製品開発等支援補助金」を活用し、信州大学工学部、長野県工業技術総合センターと連携して、「産・学・官」で取り組んだ「プレス用金型の熱処理における歪みを極小化する技術」の開発だ。「鋼を熱すれば変形・反り・曲がりなどの歪みが生じる」という人類が鉄器を使い始めた有史以前からの常識に果敢に挑戦したもので、「試行錯誤しながら19の手法を試してみたら、2つの手法に可能性を見出した」(西澤社長)。そこで、23、24年度も「戦略的基盤技術高度化支援事業(サポイン)」を活用して研究開発を継続。ついに歪みを従来の30分の1以下に抑える世界初の技術開発に成功した。
歪みが少ないと表面を研磨する際の研磨代(しろ)を少なくできるし、穴を開ける際も最小の大きさで済むので、金型を熱処理した後の工程を大幅に短縮できる。西澤社長によると、従来は半日から2日ほど要していた金型の仕上げ加工が数分から2時間程度に短縮できるという。これに伴い、金型の製造コストが8分の1以下に低減できるそうだ。この技術は新聞社や業界団体、自治体などから数々の賞を受賞。国際特許を取得するとともに、「?syori(G処理)」という商標登録で事業化し、顧客の金型メーカー及びその金型を用いたエンドユーザーに喜ばれている。
このほかにも、金型や切削工具などの材料選定から熱処理、表面改質(ショットピーニング・ショット研磨)、表面処理(コーティング)までをオーダーメードで一貫して行うことで、高性能化・長寿命化を図る加工技術「O.Nsyori(ON処理)」を提供するなど、新しいアイデア、技術を次々と生み出している。これらの創意工夫を凝らした経営にたゆまず取り組む姿勢が評価され、昨年末には「地域未来投資促進法」に基づき、地域経済を牽引する企業として国(経済産業省)から「地域未来牽引企業」に選定された。
企業データ
- 企業名
- 岡谷熱処理工業株式会社
- Webサイト
- 法人番号
- 5100001019405
- 所在地
- 長野県岡谷市南宮1-5-2
- 事業内容
- 金属材料等の熱処理、コーティング